by Tom | Dec 16, 2012 | Hardwood Floor Refinishing, South Park Modern Bungalow

Imagine this picture after 3 days of rain. Yes folks, mud, mud and more mud. It just wasn’t in my cards this week, after almost 2 weeks excavating for the driveway and setting forms, the rains came.
Had I just finished a day earlier I would have avoided a 5-day set back due to the weather. You can see I broke up the huge space by setting the forms in a more modern design for the concrete, it will do wonders for the scale of the driveway and also add an interesting modern touch.
Inside the gaps between the slabs I can put river rock, decomposed granite or even a low grass. There wont be any sod in my landscape design, the whole yard will be xeriscaped and planted with drought tolerant native species.
The unfinished cmu block retaining walls and large square concrete slabs for stepping blocks will give a real urban mod feel and be perfect for my modern bungalow.

The full custom, flat panel millworks package went in on Monday from Jed at Hollands Custom Kitchens in El Cajon. Full extension, soft close, dove tail, the whole 9 yards.
Hollands is rad, great service, quality and they’ve been building cabinets for 35 years here in San Diego. They hand built everything specifically for the house including kitchen and bathrooms. Everything will get finished on site after the install. On the uppers I used grain matching “rift cut” Red Oak.
We’ll stain them Golden Pecan to match the floors while the island and lower cabinets will all get painted a dark blueish grey. I’ll contrast the dark lowers by using arctic white quartz countertops with a square eased edge profile and waterfall on one side of the island.
In fact the counters, appliances and even carpet upstairs are all waiting to go in as soon as the floors are done.

So you can see a lot was riding on the floor job coming out on time. After 2 days of sanding, the floor guys decided to apply the oil based stain when it was raining outside and 90% humidity.
It might have actually worked even though you shouldn’t stain in higher than 60% humidity, but they tried an advanced technique called “water popping” in which you wipe the raw wood with water to raise the grain just prior to staining.
This trick is normally reserved for trying to get wood floors to accept a very dark stain or hide scratch marks, in my case it wasn’t necessary since I’m going very light and Red Oak is the easiest material to work with. Soaking the floor with water combined with the high humidity trapped in the moisture under the oil based stain and it dried looking very blotchy.
I’ve been doing beautiful Oak floors for years and we never popped the grain, I wouldn’t advise anyone to try it unless you are going very dark or have an absolute professional that has experience with popping the grain doing the work.
Needless to say I hired a different company and we are sanding off all the stain and starting over. New 3/4″ Red Oak floors only have enough thickness to refinish about 6 times, its not the best scenario to re-sand new installs twice but they’ll look perfect when we are done and that’s what counts. More on water popping hardwood floors here.
It’s really frustrating to get slowed down at the end of a project, but its just part of the business and being able to react swiftly and find solutions will keep you moving forward.
We’ll see if this week works out a little better. See you soon with concrete pics and a complete kitchen. Have a Merry Christmas and thanks for following our projects!
by Tom | Dec 2, 2012 | San Diego Real Estate Market, South Park Modern Bungalow, Tile, Tubs and Showers
We are still making progress on the Modern Bungalow trying to wrap this house up, but with the holidays its been hard to keep up the pace. Since my last update inside we got the central air conditioning installed, hot water heater, red oak stair treads and risers, and all the electrical trim and fixtures. Custom tile job.
The fire sprinkler guy came back and trimmed out too, installing all the sprinkler heads and bell box. There’s nothing left inside except for the tile setting while I wait for another week for the cabinets to arrive and get installed.
The countertop fabricator is on standby to come right in after the cabinets, then its only hardwood floor refinishing and carpet in the 2 bedrooms. Garage door is also on order. I could have had it wrapped inside by now if I would have ordered cabinets before the drywall went up.

The new tile contractor I hired is done now with mud floating all the walls and getting into tile setting with his wife. This is the second husband and wife team we’ve had on this job, my exterior painters’ wife also was a painter. Mud set tile job is the best method and common in San Diego with real tile setters.
These ladies know what they are doing too, they are not just sweeping up! Instead of Hardi backer we opted for the mud float method where you do moisture barrier paper, metal lathe and then float out the walls with spec mix. The City comes and inspects paper and lath before you can start floating the walls. Mud set is definitely the way to go.
It gives a perfectly flat and plumb surface but definitely more work, he spent 4 days floating the walls with mud when I could have put up Hardi backer board in a few hours. The tile I went with in the master is a modern 12 x 24 light grey designer porcelain and I stacked it square to give a more clean minimalist and contemporary look.
In the hall bath I went with the 3×6 ceramic but also opted not do do a subway pattern so it will be more of a clean look with a period material, working well with our home design. Both bathrooms got great niches in the wall for soap and shampoo bottles.

I thought by now I would have been done with the house but things always drag out at then end, time is on my side with Christmas and New Years coming up now so we’ll move in after the holidays.
The San Diego real estate market is still very hot. No signs of slowing even through the typically slow Fall season. With only a little over 2 months inventory it is a sellers market again and we are seeing bidding wars and multiple offers in all price tiers.
I don’t see things changing through 2013 because interest rates will stay low and there’s no more huge waves of foreclosures coming as all the adjustable loans have reset already. Banks will continue to trickle out a few REO’s here and there, but even short sale volume is dropping fast. House flippers in San Diego will have a tough time competing with large, well funded buy and hold groups investing for appreciation.
Some flippers are moving up the price range and flipping million dollar homes where there is less competition. There’s a lot of investor and first time buyer activity and prices are being affected by it, October was up 13% from last year and in some areas have reached 2005 peak home price levels again.
by Tom | Nov 17, 2012 | House Design, San Diego Real Estate Market, South Park Modern Bungalow
Just over 4 months since I poured the foundation on our Modern Bungalow, we are making progress over in South Park, walk through with me and let me know what you think. The grey interior colors might appear a little soft but don’t let that fool you.
Once I get the warmth from the hardwood floor refinishing, and my bold surprise cabinet choices, it will all work. I’m moving straight into tile now and concrete flat work outside. My electrician is trimming out and we just passed the meter inspection Friday so I can call SDG&E now to get the power moved from my temporary pole to the house. Construction rough in is complete.
Have a Happy Thanksgiving and thanks for following!
by Tom | Nov 9, 2012 | South Park Modern Bungalow
The James Hardi Siding came out really nice. exterior paint got finished last weekend, here are some pics that show how it came out. Its vivid and bold, definitely not predictable colors from the Craftsman era but leaning more modern.
The bronze aluminum windows also really give it a sort of commercial modern look and contrast well with the light trim. The stained overhangs and individually painted rafter tails are really a surprise detail not to be overlooked.
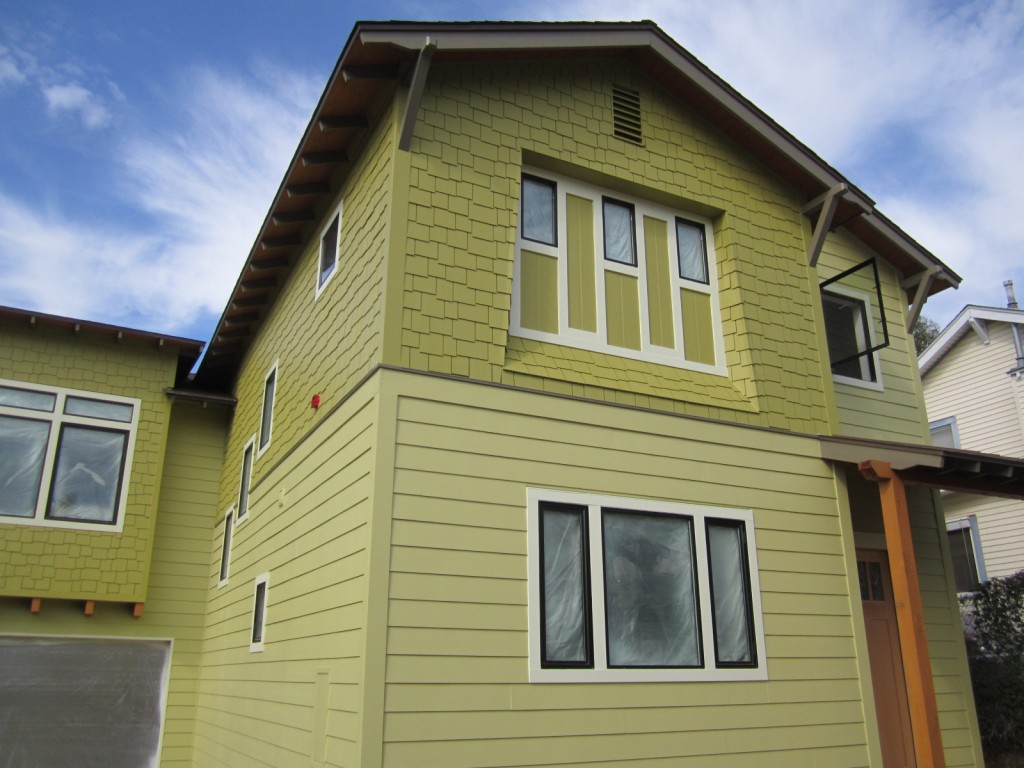
On the front porch, I went with a bronze standing seam metal roof, it ties into the windows and the main roof color. I feel that I got a really good deal at 700 bucks and my sub contractor hand made it on site.
The cedar porch posts and beam were also stained to match the eaves. The visible T&G under the porch is also stained to match the eaves, I’ll show this detail later with a better pic.
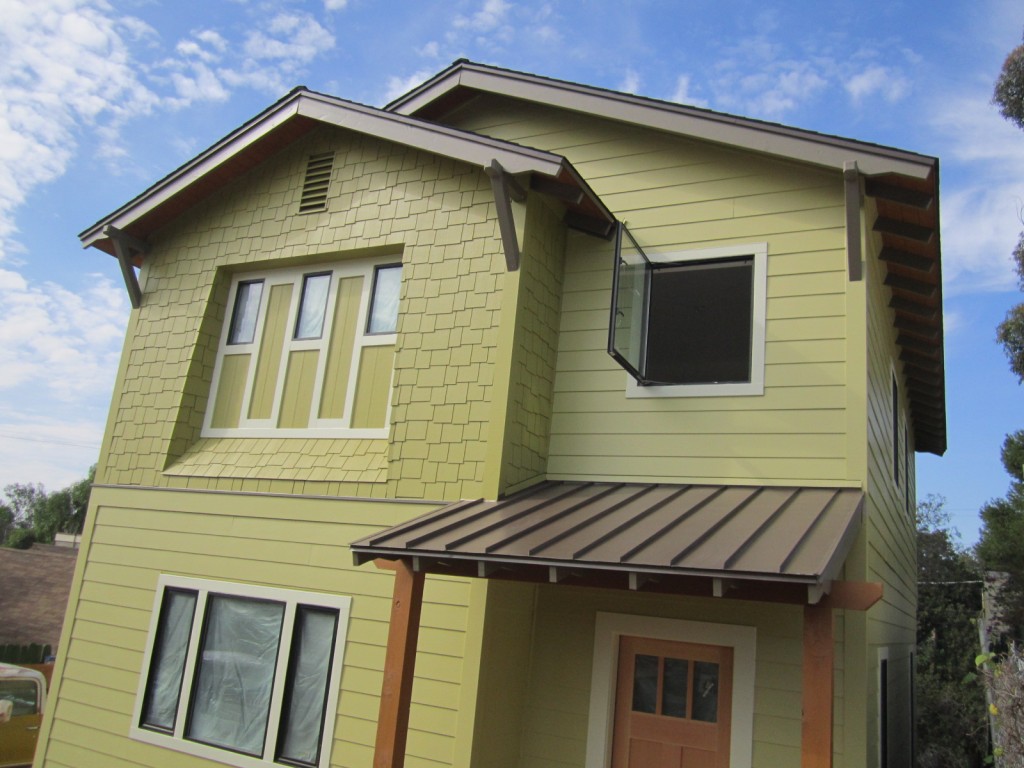
While the house was getting painted outside, I was inside trimming it out. I went with the Craftsman style 3-panel doors this time. Its the first time I’ve used them and they are pretty swell, especially the 8 foot high ones and the parlor doors on the bedroom closets.
Even the water closet pocket doors are the same style. I used 8″ baseboards and 4″ door casings. There are only 2 bedrooms that will get carpet, you can see I left the baseboards up 1/2″ off the floor in those rooms.
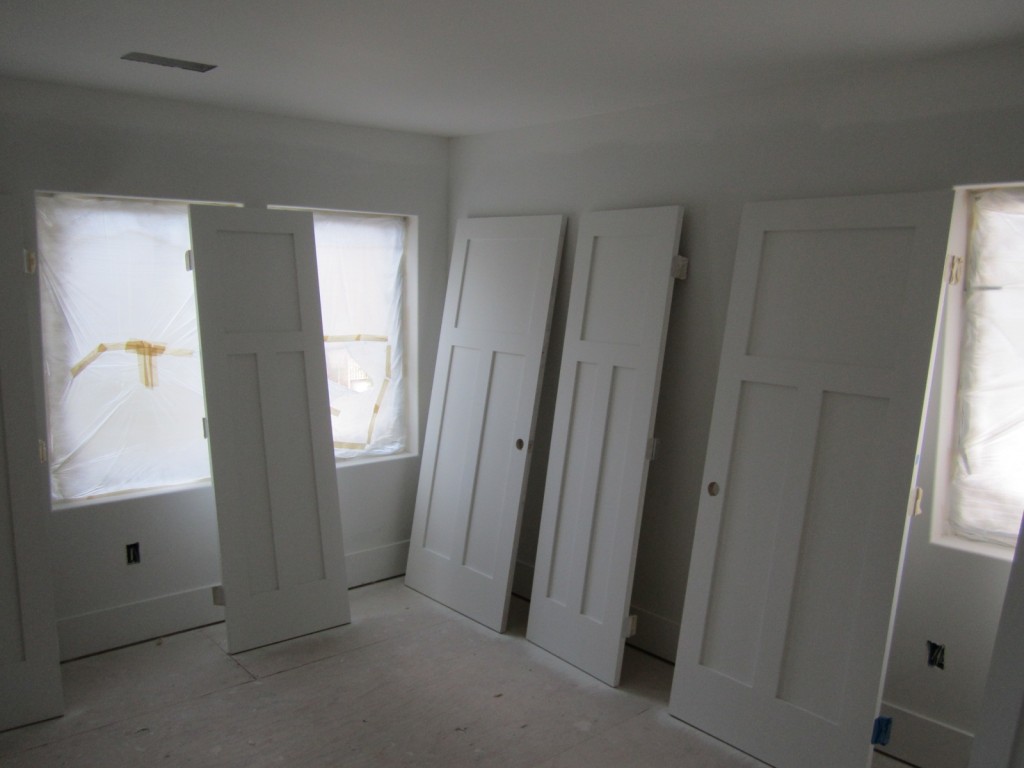
Here is the order I do interiors in: 1. Hang Drywall 2. Install Hardwood floors 3. Trim out 4. Spray Ceilings 5. Spray trims 6. Paint walls 7. Tile 8. Install Millworks 9. Refinish Hardwoods 10. Carpet.
When painting ceilings and walls I love coming with a roller behind the sprayer, your coat comes out way nicer and the roller pushed the paint into the new drywall. I also use PVA drywall primer on the new drywall. Everything always gets 2 coats as well.
There are other methods that work too, I’ve seen guys actually put the wall color on before trimming out the house and hanging doors. Then they come back and just paint the trim. For me I think it causes too much touch up later and the dust inside the house when you are cutting all the MDF trim gets everywhere.
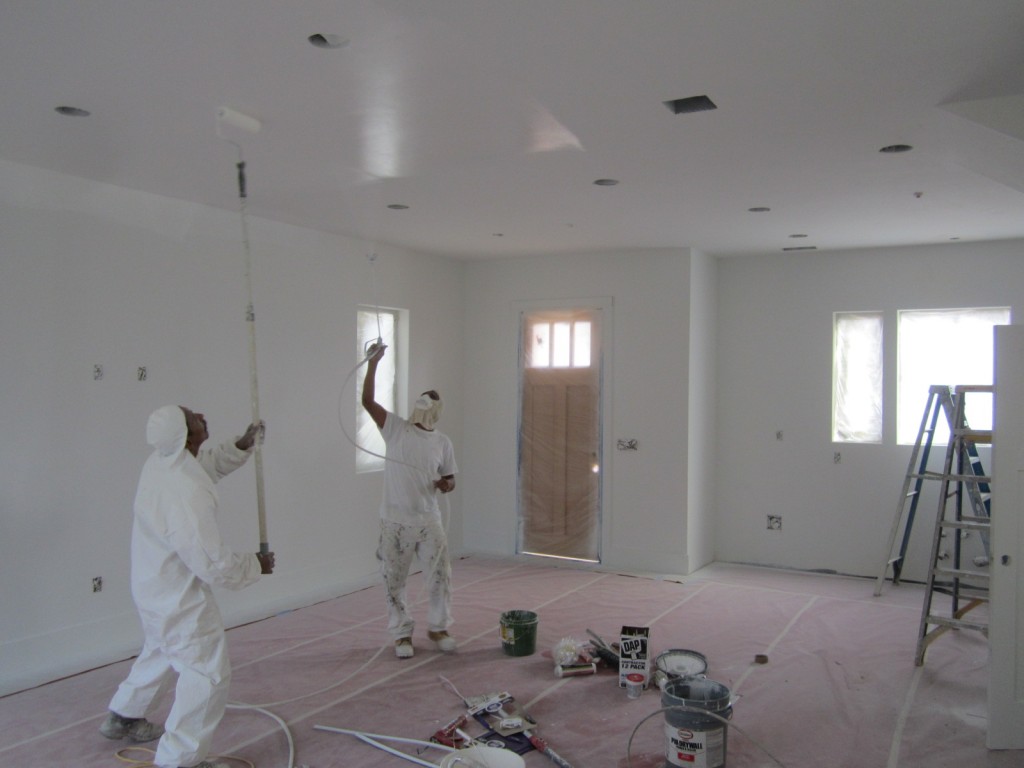
You can see the guys spraying the ceiling and back rolling while still wet. I’m trying a lot of new things on this project with the interior paint colors and finishes and reversing lights and darks in a way most people don’t see. Its always more work to try new ideas but challenging and rewarding to keep progressing.
I am doing a fully custom millworks package (cabinets) for the whole house. Its on order and getting built, should arrive around the end of this month. After the interior paint we will move into the tile jobs inside and the concrete driveway, small retaining wall and flatwork outside.
by Tom | Nov 4, 2012 | Exterior Paint, South Park Modern Bungalow

Here’s a sneak peak of the exterior house colors and paint job on our Modern Bungalow. You can see the color choices are bold and edgy, playing into our contemporary design twist and coming out just as I planned.
I didn’t pull the window trim color all around the house to the corners and smaller areas intentionally to give it a more mod feel, it worked well as there is enough detail already in the siding design without the extra coloring. For me the stained eaves and dark rafter tails really do it.
Exterior house colors are all satin and as follows: Body SW Wheat Grass, Shingles SW Edgy Gold, Trim SW Ionic Ivory, Rafters and tails Cromwell Grey, Eaves Behr semi-transparent Natural Cedartone. Next, we are moving inside to the interior paint and tile.